OPERATE JAMES STREET -
Click here
OPERATE JAMES STREET -
Click here

Ship 3 - 'JAN WILLEM'

The next ship to be built was the green hulled JAN WILLEM, representing a motor coaster of the late 50s-early 60s, many of which were Dutch family-owned ships, with the owner also often being captain. They were known in the UK maritime industry as 'skoots', after the Anglicised pronunciation of the Dutch classification 'schuyt'. Later versions built from the 80s onward are for some reason known as 'sea snakes' in the UK!
The basis of the model is another 'Shell Welder' hull, and again, the hull was glued together, then cut along the waterline, and a reinforcing base added. A mix and match of some parts of the kit were used to make the accommodation and wheelhouse. A new main deck was cut from plastic card, fitted, and then hatch coamings (sides) and covers (tops) were made from various plastic card, angles, rods and strip. Ladders are plastic mouldings. The masts and derricks are made from soldered brass tube and wire; the topping lift wires used to raise and lower the derricks were also modelled using wire, as I wanted to model the catenary of the wire when rigged for sea. It is impossible to get this as a straight line as in reality the tension is too high. (Think of a linen line at home)
I haven't modelled a cargo for the ship, as on the layout, it represents a ship just arriving at the berth and making fast to the quay, often with the model tug assisting. This type of ship carried a wide variety of cargo, including mixed general, grain, bulk powder or ores, coal, timber, and many others. Often, they also carried a deck cargo on the hatch covers, particularly in the timber trade, but not in the case of the model.


Ship 4
The next ship again used the 'Shell Welder' hull. It was decided to model a general cargo ship with two hatches, of which there were a number of variations in details when built.
Much as the 'Jan Willem' was built, after fitting the main deck, openings were drilled to open out the solid 'deck' and make the hatch openings so that a cargo could be modelled inside the hold. Also, the hatch coamings were again scratch built from plastic shapes and sheet. I decided to make the hatch covers as the older pattern of small hatch boards which were manhandled into position by the dockers or crew and rested on beams from side to side of the hatch. When the hatches were closed and the boards in place, they were then covered with tarpaulin sheets. I modelled these boards and tarpaulins as open and stowed away from the cargo working area, ready to be refitted when needed. The individual boards were cut from plastic planked sheeting and then painted. Cargo winches were plastic commercial mouldings.

I made a different funnel for this ship by simply cutting an appropriate length of plastic tube. Masts are made from brass tube and wire. However, I decided that I would rig the ship as if one of the hatches was being worked by the then common method of 'union purchase rig'. This involved two derricks rigged to a common cargo hook and swung so as one derrick plumbed the ship's hold and the other the shore cargo landing area. Rigging for the derricks was by wire, but for the cargo hook 'runners' were made from cotton thread. To say this was fiddly and time consuming is a large understatement…., but I got there eventually! The second hatch is modelled as if worked by shore crane(s). Cargo is from commercial products.



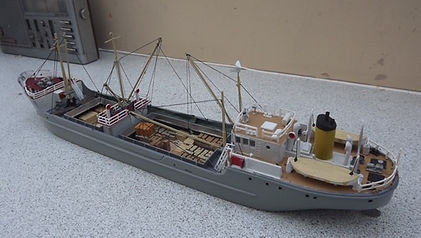
This completed the first batch of building for the original dock.